It has also become apparent that the high current power supply not being current limited has destroyed the +12 Vdc on the PCB at least 5 times! This is probably due to poor constructional technique (my bad soldering) and the tracks not being thick enough to carry the amount of current present in normal operation. I was playing with the circuit last night after having put the high voltage probes into a laser cut case (which worked perfectly) I managed to catastrophically damage components...Standard form for me to be honest....that is why I call this prototyping!
The issues I'm having are all to do with construction and design choices that I made when I initially designed the plasma speaker PCB. I'm going to design a new version which improves the situation:
- Increase current rating of all tracks carrying +12V or GND.
- Incorporate the Class A amplifier into the circuit so that everything is on one PCB
- Increase the gain on the Class A amplifier as it still (in my opinion) is not loud enough
- Move the components which get incredibly hot off the PCB and onto the heatsink.
First off I think I really need to find out just how much current the main switching transistor is subjected to. This is going to involve checking the datasheet for the transistor and performing some ohms law. I hate maths but in this case it has to be done...I cannot assume all will be well if I don't check the current requirements of the 12 Vdc conductor.
Here is the new schematic with all of the circuitry on one sheet:
The datasheet for the IRFP250 is here:
From the datasheet we can see that the RDSon parameter of the transistor is 0.085 ohms. If we assume that the dc resistance of the flyback transformer is also quite low then the amount of current constantly present as the transistor switches will be high...The energy from the flyback voltage at the primary must also be taken into account.
In order to discuss this I should really link in a page discussing how flyback transformers function:
EE Times article on flyback transformers
Wikipedia Entry on Flyback Transformers
My schematic diagram has not ever shown the actual flyback transformer which is actually a transformer with 10 turns on the primary core and several thousand turns on the secondary core which is then connected to an internal 'flyback' diode and capacitor.
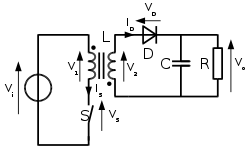
Basically what this means is that the output of the transformer and associated energy output is related to the winding ratio, the capacitor and the load applied at the output which in this case is an arc through the air.
For the purposes of calculating how much current will be flowing in switching transistor part of the circuit I'm going to simulate the circuit. The reason for simulating is that it's quicker for me than calculating all of the Ohms law required on paper....Here is the circuit after simulating:
Well....that explains why the MOSFET Q3 got so hot and needed such a large heatsink along with the flyback diode D1 and the 120 Ohm resistor....1.6A constantly flowing in that part of the circuit is a great deal and also explains why the 12 Vdc conductor and the conductors in the FET part of the circuit needs to be as thick as possible. I have made assumptions on the turns ratio of the transformer but it doesn't really matter as I have seen from the power supply current meter that I'm using to power this circuit that these calculated current values are close enough....Therefore the design needs to account for this 2 Amp current being present - I actually think the instantaneous peak currents will be considerably higher than this and the current is also higher when the audio modulation is applied.
To that end we need to redesign the PCB to take this into account. Here is the new PCB layout:
I then etched and populated the PCB. I have found that the circuit works better but still had some issues. I have mounted the 120 ohm 5 Watt resistor on the heat-sink along with the clamp diode which I have swapped for a TO220 packaged version. I also changed the operating frequency of the 555 oscillation by changing the value of C1 (in the uppermost schematic) to 100 pF. This changes the oscillation frequency to somewhere always above 20 kHz which removes an annoying high pitch whistle when the circuit is in use.
There are still issues with the circuit but I believe this is now as good as it will probably get. I need to obtain a suitable high current power supply and mount the circuitry properly to make it easier to move around. I have had a lot of fun developing this circuit and visually it's really attractive. It's practicality is exceedingly limited. A plasma speaker loses a great deal of fidelity with low frequency bass sounds, generates significant amounts of ozone, uses a large amount of electrical power and is fundamentally dangerous because of the high voltage DC that is present.
Here is a video of me playing around with it using an electronic keyboard to provide the audio input.
That's all for now - take care people, especially with high voltage dc circuits and plasma speakers!
In order to discuss this I should really link in a page discussing how flyback transformers function:
EE Times article on flyback transformers
Wikipedia Entry on Flyback Transformers
My schematic diagram has not ever shown the actual flyback transformer which is actually a transformer with 10 turns on the primary core and several thousand turns on the secondary core which is then connected to an internal 'flyback' diode and capacitor.
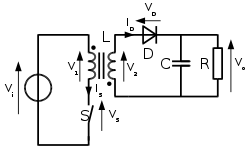
Basically what this means is that the output of the transformer and associated energy output is related to the winding ratio, the capacitor and the load applied at the output which in this case is an arc through the air.
For the purposes of calculating how much current will be flowing in switching transistor part of the circuit I'm going to simulate the circuit. The reason for simulating is that it's quicker for me than calculating all of the Ohms law required on paper....Here is the circuit after simulating:
Well....that explains why the MOSFET Q3 got so hot and needed such a large heatsink along with the flyback diode D1 and the 120 Ohm resistor....1.6A constantly flowing in that part of the circuit is a great deal and also explains why the 12 Vdc conductor and the conductors in the FET part of the circuit needs to be as thick as possible. I have made assumptions on the turns ratio of the transformer but it doesn't really matter as I have seen from the power supply current meter that I'm using to power this circuit that these calculated current values are close enough....Therefore the design needs to account for this 2 Amp current being present - I actually think the instantaneous peak currents will be considerably higher than this and the current is also higher when the audio modulation is applied.
To that end we need to redesign the PCB to take this into account. Here is the new PCB layout:
![]() |
Top Layer Of PCB |
![]() |
Bottom Layer of PCB |
![]() |
Both Layers with Dimensions |
I then etched and populated the PCB. I have found that the circuit works better but still had some issues. I have mounted the 120 ohm 5 Watt resistor on the heat-sink along with the clamp diode which I have swapped for a TO220 packaged version. I also changed the operating frequency of the 555 oscillation by changing the value of C1 (in the uppermost schematic) to 100 pF. This changes the oscillation frequency to somewhere always above 20 kHz which removes an annoying high pitch whistle when the circuit is in use.
There are still issues with the circuit but I believe this is now as good as it will probably get. I need to obtain a suitable high current power supply and mount the circuitry properly to make it easier to move around. I have had a lot of fun developing this circuit and visually it's really attractive. It's practicality is exceedingly limited. A plasma speaker loses a great deal of fidelity with low frequency bass sounds, generates significant amounts of ozone, uses a large amount of electrical power and is fundamentally dangerous because of the high voltage DC that is present.
Here is a video of me playing around with it using an electronic keyboard to provide the audio input.
That's all for now - take care people, especially with high voltage dc circuits and plasma speakers!
No comments:
Post a Comment